Industry 4.0 is set to be the biggest driver of manufacturing innovation and efficiency since the introduction of automation – but what does it mean, what impact is it set to have and how can you start to evaluate the benefits for your business?
In this post we’ll take a look at some of the key drivers, statistics and facts behind Industry 4.0 and explain why simulation is being increasingly used by manufacturers as a tool to assess implementation.
What is Industry 4.0 and where did the term come from?
The term was coined in 2011 as ‘Industrie 4.0’ by a German government strategy group researching the future of manufacturing computerization.
So why Industry ‘4.0’? It refers to the fourth industrial revolution – the latest in a series of historical technological advancements that have transformed manufacturing.
The first revolution began with the invention of steam-powered mechanical production in the 18th century, with the second arriving in the early 20th century as electricity gave rise to mass assembly line manufacturing.
More recently in the early 1970s, advances in automated production using robotics triggered the third industrial revolution. Now, we’ve entered the age of the ‘smart factory’, where robotics and computer systems are converging to operate and make decisions with minimal input from human operators.
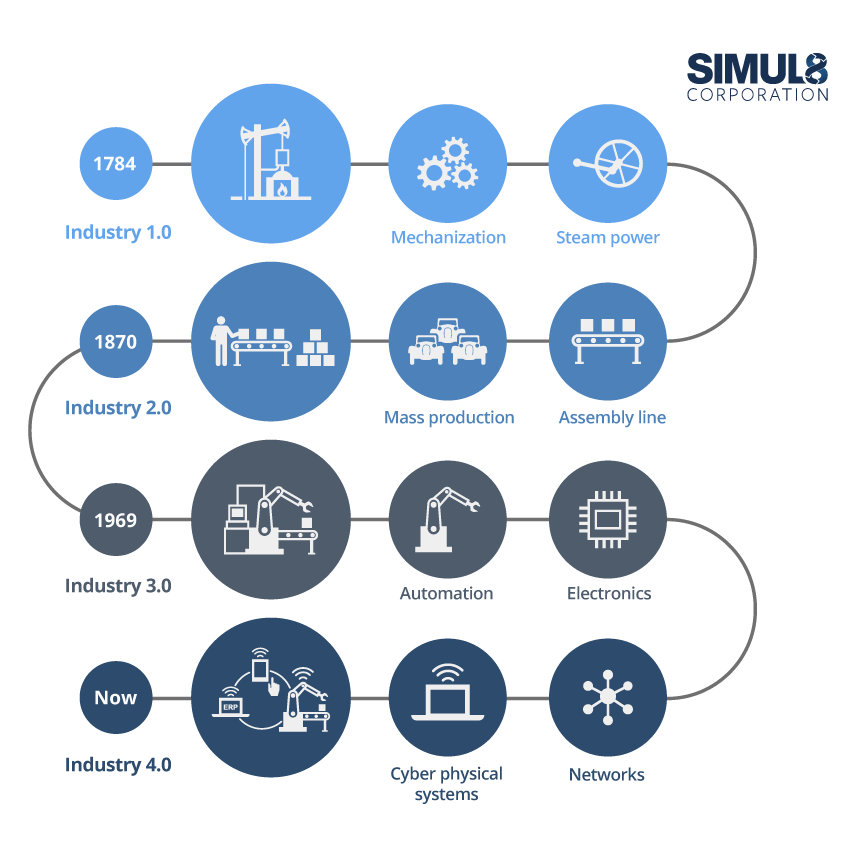
The four industrial revolutions
So what exactly makes a factory ‘smart’? There are four key guiding principles of Industry 4.0:
- Interoperability
The ability of devices, vehicles, buildings and people to communicate and process information with each other via the Internet of Things (IoT). - Information transparency
The creation of a virtual copy or ‘digital twin’ of the physical world using sensor data to represent a whole system – for example, a manufacturing plant or contact center. - Technical assistance
The use of information tools to support decision making through the rapid aggregation and visualization of process data, as well as physical tools that help or replace human effort for demanding or dangerous tasks. - Decentralized decisions
The ability for computer-based systems to make their own decisions for regular events in a system, only seeking human oversight when an exceptional or confusing event occurs.
What economic impact could Industry 4.0 have?
Research by Accenture estimates that Industry 4.0 technologies like the Industrial Internet of Things (IIoT) could add as much as $14.2 trillion to the global economy by 2030.
With huge potential economic benefits, many countries around the world are offering funding and incentives to help spur the adoption of Industry 4.0 technologies.
For example, in the US, technology firms, manufacturers, suppliers, government agencies and universities have formed the Smart Manufacturing Leadership Coalition, a not-for-profit-organization funded by $140m of public and private investment.
In Europe, Germany has committed €500 million to encourage the research and development of Industry 4.0. It has also been highlighted by the UK government as an area of focus to boost productivity and the economy – with £4.7 billion of funding being made available for research and development into robotics, artificial intelligence, 5G mobile technology and smart energy.
What are the key benefits of Industry 4.0 for manufacturers?
Effective implementation of Industry 4.0 can offer a number of benefits for organizations, including:
- Productivity and efficiency gains
Smarter equipment enables more agile and effective manufacturing decisions to be made – allowing for faster, more efficient production that can operate around the clock. In a survey conducted by The Manufacturer in 2017, 80% of respondents expected that connected factories would help to increase output. - Improved reliability and quality
As production issues can be found much faster and corrective changes automatically made by machinery, this helps enhance the quality and accuracy of production. With improved connectivity and data, manufacturers can utilize these to optimize processes and enable closer collaboration along the entire supply chain to improve quality and reliability. - Increased profit margins and reduced operational costs
Although Industry 4.0 technologies often need large up-front investment, they can reduce waste, inventory and operating costs within a few years of implementation. The ability to perform predictive and preventive maintenance and upgrades enables manufacturers to reduce the impact and costs associated with things like downtime and changeovers. Capgemini’s Smart Factories report suggests that for an average US-based car & truck manufacturer, the productivity and efficiency benefits of smart factories could improve operating margin as much as 10.4% within five years. - More flexibility and ability to innovate
Smart production lines improve flexibility to be able to handle high-mix and low-volume production, in turn, enabling manufacturers to experiment with different product designs and configurations. This can also help organizations to improve competitiveness through the ability to offer more diverse, personalised product ranges. - Better customer experiences
With access to usage data from connected machinery and products, manufacturers can continually improve their products and offer faster, more proactive customer service.
Companies are starting to invest in Industry 4.0…
According to PwC research, companies are set to invest $907bn in Industry 4.0 products each year through to 2020.
This investment will include the robotics and equipment needed to drive smart factories, such as sensors and connectivity devices, as well as software and applications like Manufacturing Execution Systems (MES) which will enable machinery to make autonomous decisions.
In addition to investments in equipment and software, manufacturers will also have to invest in training for employees and initiatives to drive the organizational change needed fully realize the opportunities associated with Industry 4.0.
… but some also have concerns
Although Industry 4.0 does offer organizations a range of benefits, there are also some concerns and uncertainty surrounding the movement.
Costs can be a major barrier due to the large up-front investment needed for equipment, software and staff training. In The Manufacturers’ Annual Manufacturing Report 2017 64% of survey respondents had concerns about initial development costs involved in implementing or continuing to use forms of factory connectivity, with 36% being unsure when or if they would see a return from investing in these technologies.
Could simulation help you to assess the potential of Industry 4.0?
The future is promising for Industry 4.0, but organizations need to decide what they want to achieve from these technologies and select the most effective route to get there.
With high initial costs, as well as many changes to processes, staff and suppliers to consider, many manufacturers want to thoroughly evaluate the business case for Industry 4.0.
At SIMUL8, we are seeing more and more of our users considering the use of Industry 4.0 related technologies like AGVs drones, sensor technology and 3D printing. But every manufacturing system is unique and there is no one-size-fits-all approach to implementing these technologies. The use of simulation software gives organizations the ability to evaluate Industry 4.0 principles and technologies in a risk-free, virtual environment to find the answers needed to make confident decisions ahead of any investment.
Ready to learn more? See examples of how SIMUL8 has been used for Industry 4.0 projects or contact our team to discuss your specific project goals.