Written by Frances Sneddon on Thursday August 8th 2013 in Art of Simulation, Latest News, Simulation Solves, Technical Corner
In Lieu of Money, Toyota Donates Efficiency to New York Charity
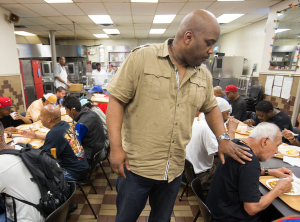
I was completely inspired this week reading an article in the New York Times about how Toyota have used their Lean skills to help The Food Bank for New York City improve their efficiency.
Toyota’s engineers have cut down the wait time for dinner at the soup kitchen from 90 minutes to just 18. At a food pantry on Staten Island, they reduced the time people spent filling their bags from 11 minutes to 6. And at a warehouse in Bushwick, Brooklyn, where volunteers were packing boxes of supplies for victims of Hurricane Sandy, a dose of Kaizen cut the time it took to pack one box to 11 seconds from 3 minutes.
Lean is all about getting the best service for the customer and why shouldn’t that apply to those in need too? Best of all it means more good can be done for more people in need.
Understandably the charity was apprehensive, how could a car manufacturer help them run their kitchen? So just like starting out with Lean in many organizations they had to convince the charity it could work and they could help. They did this by meeting a “prove it” challenge set by the Food Bank.
“The line of people waiting to eat is too long,” Mr. Foriest said. “Make the line shorter.”
Toyota’s engineers went to work. The kitchen, which can seat 50 people, typically opened for dinner at 4 p.m., and when all the chairs were filled, a line would form outside. Mr. Foriest would wait for enough space to open up to allow 10 people in. The average wait time could be up to an hour and a half.
Toyota made three changes. They eliminated the 10-at-a-time system, allowing diners to flow in one by one as soon as a chair was free. Next, a waiting area was set up inside where people lined up closer to where they would pick up food trays. Finally, an employee was assigned the sole duty of spotting empty seats so they could be filled quickly. The average wait time dropped to 18 minutes and more people were fed.
Processes are just processes, doesn’t matter whether it’s making cars, treating patients, or serving food. It never ceases to amaze me how you take the lessons from Lean and apply them anywhere.
The power of Lean is to make process improvement simple, or at least consumable by all. As process improvers we see processes and their inefficiencies everywhere (especially when I watch my husband cook the dinner!). It’s a skill we take for granted. For others they don’t even recognize what they do is a process. I’m sure this is why The Food Bank were so shocked to learn Toyota could help them.
We see the building blocks and work out how we can reorder them. “Normal people” see a problem that needs to be quickly fixed and do everything and anything to keep that process running. Their dedication and hard work keeps bad processes going unfortunately.
But the real reason this article inspired me is that I’m passionate about wanting to give something back. Like others I suspect find it hard to see a place where I can add value, especially given the pressures of day to day life. But here with a Kaizen blitz is a way for us to make a quick and huge difference, doing what I do best, improving processes.

Want to chat simulation? Get in touch!
Frances Sneddon, CTO SIMUL8 Corporation
frances.s@SIMUL8.com
@FrancesSneddon