Achieving $100,000 in Savings Annually: HP’s Simul8 Success Story
Simul8 / May 15, 2024
Hewlett Packard, a global leader in electronics manufacturing, has been harnessing the power of Simul8 simulation software for over a decade. Their goal? To improve production throughput, optimize process times, and increase profitability. HP’s success story showcases how they used Simul8 to save $100,000 annually while identifying other quick-win productivity gains.
HP’s assembly and test process for their test and measurement products was facing challenges, with complex factors such as cycle times, machinery failure rates, labor availability, shift patterns, and storage capacities affecting production. To address this, they used Simul8 to model the process and identify the best setup for the production line.
Ian Harrison, QMD at HP, explained how Simul8 helped not only meet their objectives but also highlighted areas of inefficiency and opportunities to eliminate non-value-adding activities. “Simulation is particularly speedy at highlighting the major constraints within critical processes and thus enabling the model builder to construct the correct event sequence and buffer sizes to keep the major constraints fully utilized”.
Finding a Solution
The impact of simulation at HP extended beyond this single project. The use of Simul8 within the QMD Process Engineering team grew rapidly, with the number of simulation users quadrupling in just 12 months. This growth was fueled by Simul8’s comprehensive, intuitive, and easy-to-use features, which made it accessible to a wider engineering and management audience.
The simulation also served as an effective training tool, illustrating management fundamentals such as Goldratt’s theory of constraints and the need for Kanban.
“By dispersing simulation into the rest of the engineering community and first-level management, many more processes are analyzed and improved.” – Ian Harrison
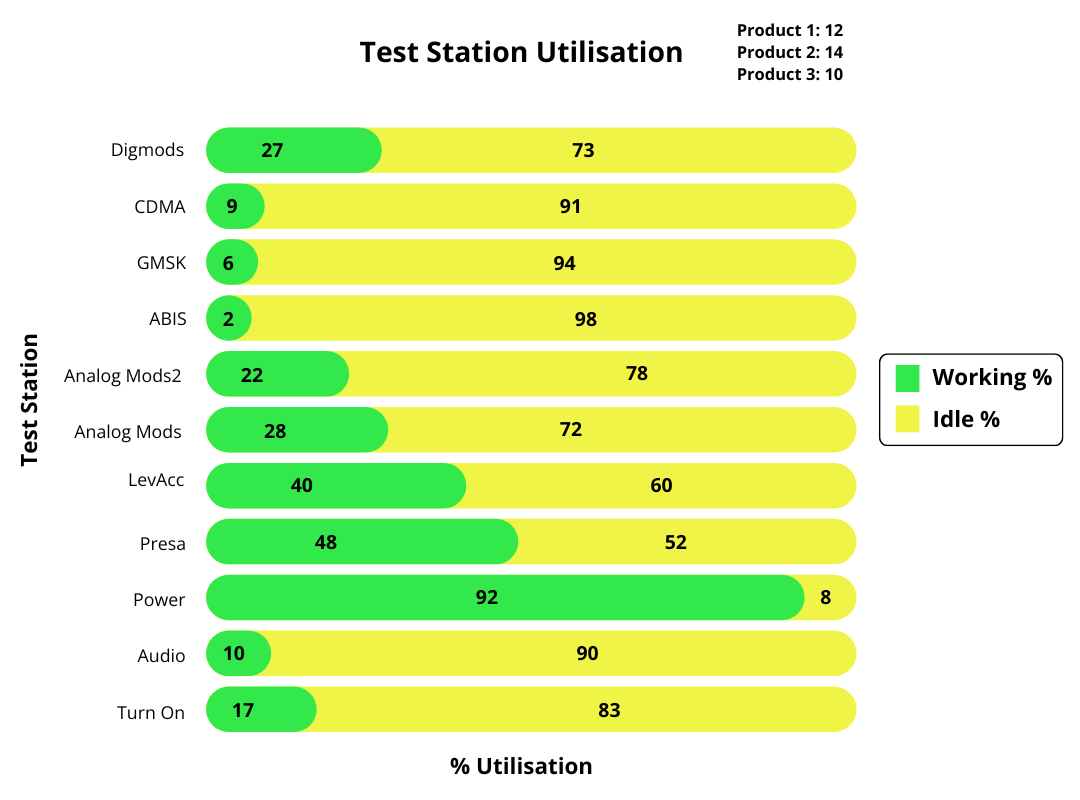
Building the Simulation
For HP, the benefits of simulation were clear. Simul8 provided a platform where simulation became more familiar and easier to use as a desktop productivity tool. The project saved HP an estimated $100,000 annually in opportunity costs, with additional productivity gains achieved through the identification and elimination of inefficiencies.
A New Way Forward
HP’s success story is a testament to the power of simulation in driving operational efficiency and cost savings. By leveraging Simul8, they were able to overcome production challenges and set the stage for ongoing improvements.
Key Takeaways
- Enhanced Production: HP used Simul8 to improve throughput and reduce process times, achieving significant efficiency gains.
- Substantial Savings: The project saved HP $100,000 annually, demonstrating the financial impact of effective simulation.
- Rapid Adoption: The use of Simul8 grew rapidly within HP, highlighting the software’s intuitive and user-friendly design.
- Training Benefits: Simulation served as an effective training tool, illustrating key management concepts and fostering continuous improvement.
- Strategic Alignment: HP’s use of Simul8 aligns with the goals of those focused on efficiency and profitability, showing the strategic value of simulation.
Interested in achieving similar results? Discover the secrets behind successful simulation projects with our free Art of Simulation Playbook. Learn how simulation can transform your business and lead to better decision-making, faster.