Pallet optimization with simulation
Most manufacturing facilities have some sort of system that uses a platform, carrier, or pallet to carry the product as it is being assembled. These systems are often referred to as a Palletized Loop; as they include an empty pallet return upon completion or transfer to another type of carrier system.
The pallet usually consists of dimensional control equipment to ensure accurate alignment with the facility’s tooling. In other words, these are not the wooden slotted pallets used in shipping. For example, a single automotive pallet can cost over $20,000 and there can be over 300 pallets within the loop! This now becomes a 6 million dollar investment for the facility. Even if your plants pallets are far less expensive than an automotive facility, it still is important to have the optimal number within the loop to ensure maximum throughput.
Why simulation?
Palletized loops need room to expand and contract to ensure optimal throughput; delays due to downtime or changeovers can degrade performance. We need to ensure that an empty pallet is available and ready for the next build, yet not blocking the transfer machine. Simulation is the best solution for visualizing your palletized loops and all of their interconnections. Simulation provides data-backed solutions to your capital investment; pallets and carriers add-up fast!
Let’s take a detailed look on how to accomplish simulating palletized loops using SIMUL8.
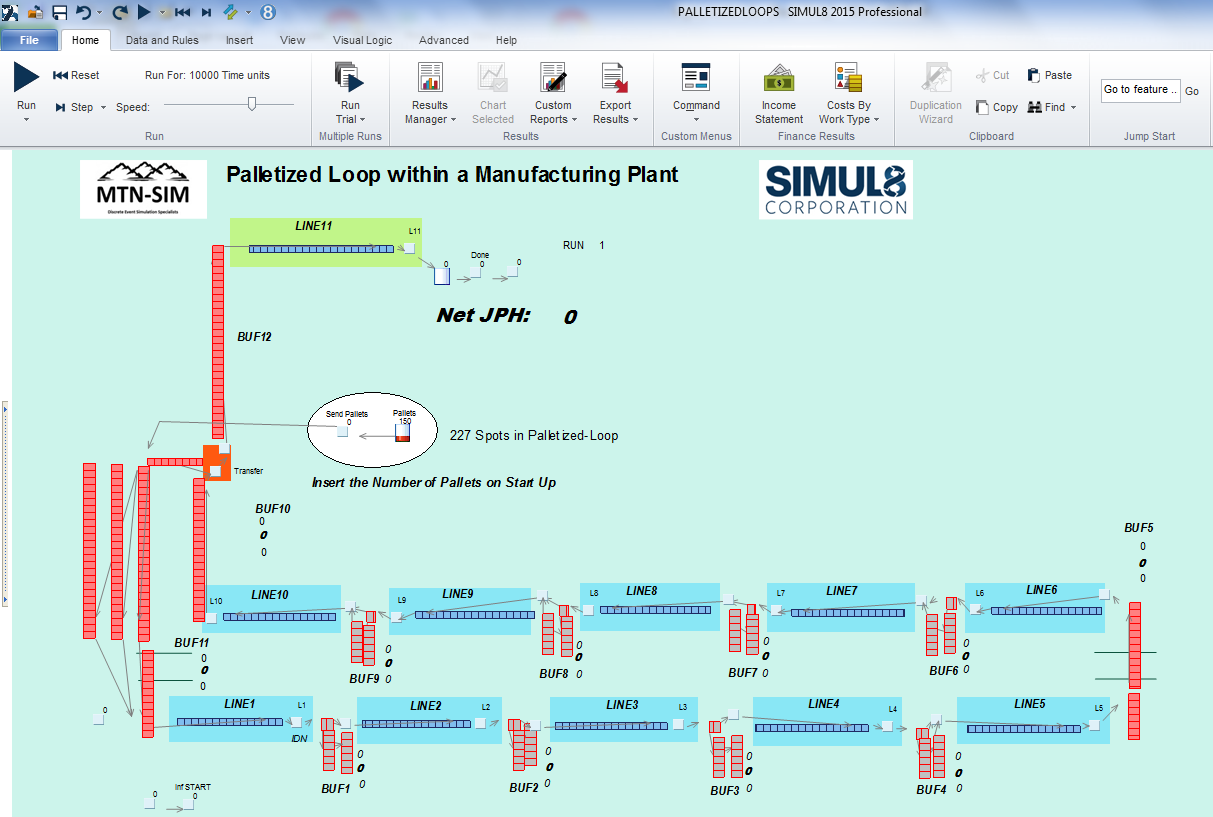
The layout
We will use one “Work Item Type” and use three unique images to represent an empty pallet, loaded pallet, and transferred part. The palletized loop will consist of 10 assembly lines separated by inline buffers. The buffers between assembly lines will maintain part sequence and hold up to 8 parts. The empty pallet return conveyors can hold up to 57 pallets. There are a total of 227 spots for a pallet to reside within the palletized loop.
It’s always a good idea to know how many physical pallets can reside within the system; even though we would never run at that rate due to system gridlock.Once a loaded pallet has completed “Line 10” it then travels to a “Transfer” machine where it transfers the product to another conveyance system. The transfer machine also sends the empty pallet to the empty pallet return lanes. All of the lines are running at 60 Jobs per Hour and have associated downtime within the lines. This information is summarized within a SIMUL8 spreadsheet “ss_Input”.
Pallets are entered into the system through a SIMUL8 Queue on “Start-Up”. This is where we perform the sensitivity analysis on obtaining the optimal number of pallets within the loop.
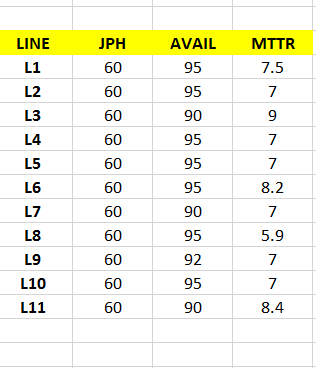
The analysis
The objective of this simulation is to obtain the optimal number of pallets in the system. We simply now run the simulation several times changing the number of pallets each run. A logical step size might be adding 10 pallets per run; hence we can develop a table which covers from 100 to 200 pallets. We will be basing our performance criteria on maximizing throughput (JPH). We can also keep track of the performance of buffers between lines. The simulation displays 3 values per buffer which represent (minimum, average, and maximum) contents.
Robust operating range

Additional considerations
We might also want to test the buffer size to Line 12. This is outside of the palletized loop; but if it is sized too small it can block the performance of the palletized loop at the transfer machine. Another common complexity that may arise in the future; a new product which requires a unique pallet. This causes sequencing complexities and optimizing 2 pallet types within the loop.
These types of carrier systems are very common within most manufacturing facilities; and they should be monitored regularly to ensure maximum performance. Simulation will greatly aid and lead the facility’s control plans and can provide a solid data-backed answer.
Learn more about using SIMUL8 for manufacturing process improvement
Find out more about how simulation is used by manufacturing organizations, read more case studies and access a range of learning resources.